Plastics occupy a major place in today's society, yet they remain an often misunderstood commodity.
We'd like to introduce you to our core business and our environmentally-friendly production process.
Plastic injection molding is a process involving several key stages.
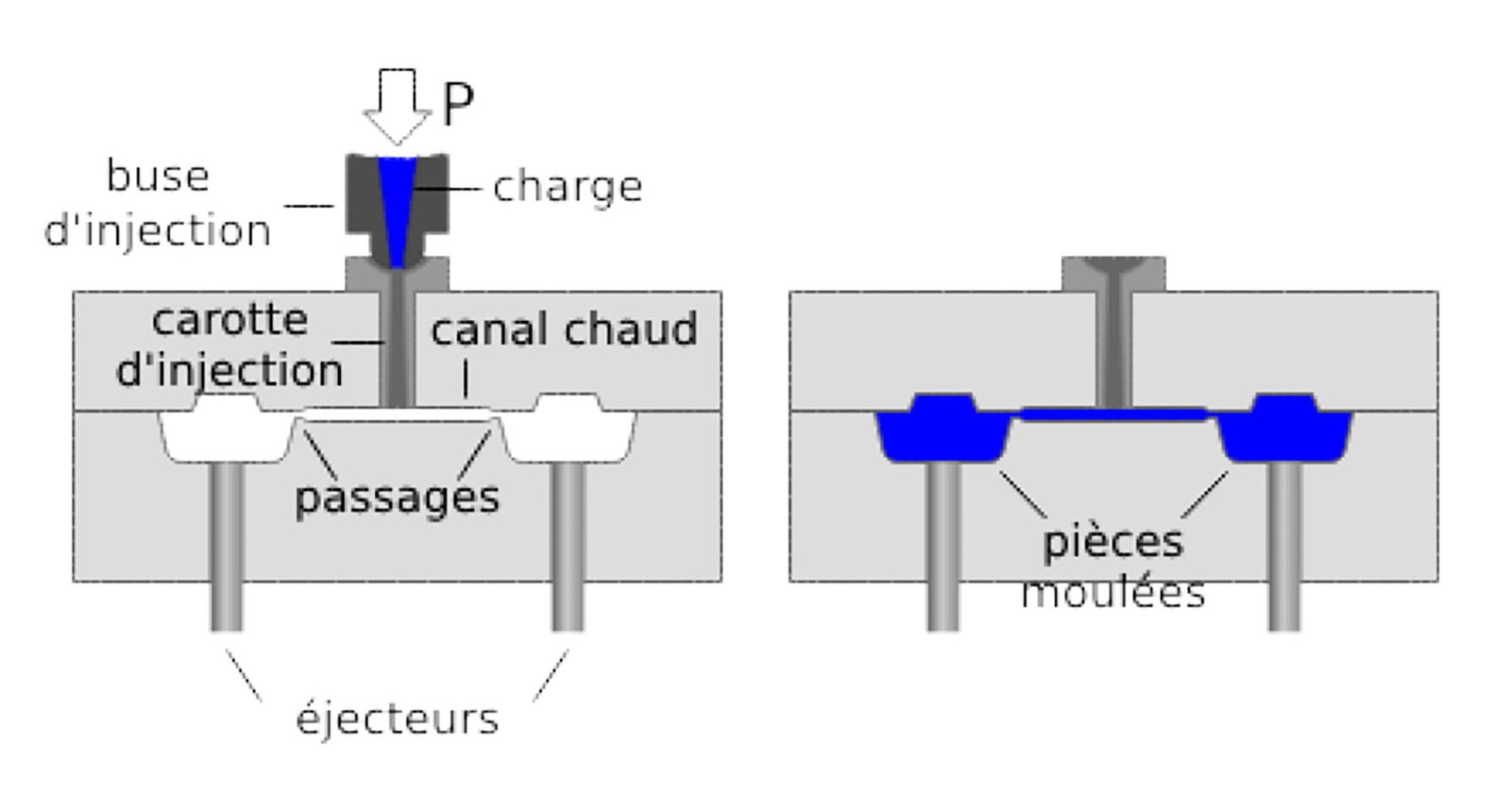
First, our injectors receive the raw material in the form of plastic granules. Their job is to transform it by injecting it at high temperature into our molds, then cooling it so that the part firms up.
Video demonstration of the manufacturing process of our cases:
Our card covers are then sent to our partners (ESAT, prisons, etc.) for assembly.
This has the advantage of creating jobs while promoting social inclusion, unlike, for example, ultrasonic soldering. The latter, although inexpensive, is difficult to master and can vary from one production run to another (the card may get stuck or fall out of the case). The manual assembly method also consumes less energy.
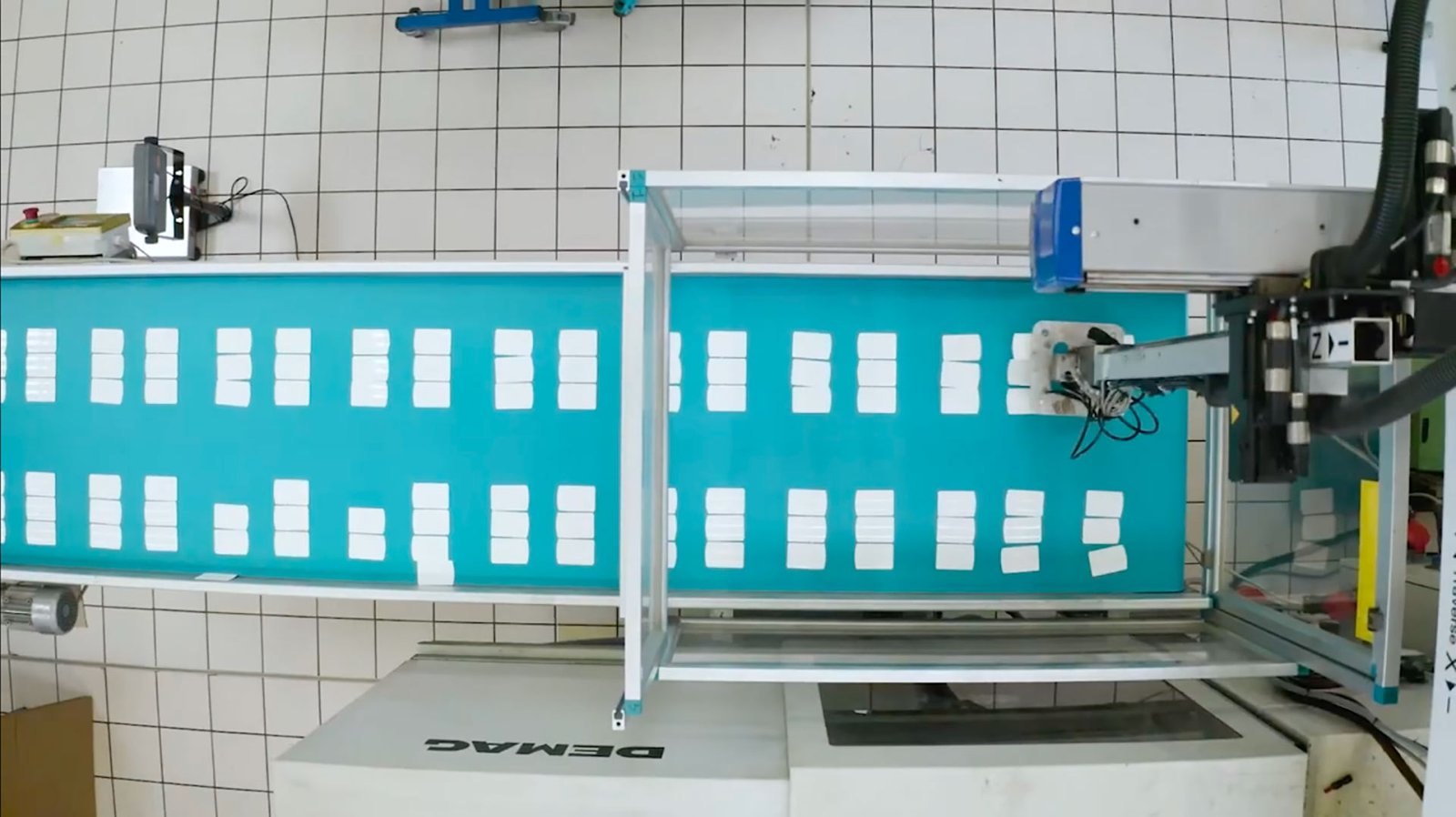
Cooling phase of ClickCarteTM on the conveyor belt after injection
As a company in the plastics industry, it's essential to control our waste and any discharges.
The injection plant for a large proportion of our models is a signatory to the Operation Clean Sweep program. This program provides guidelines and concrete actions to prevent the loss of plastic pellets into the environment.
For example, to prevent risks in the event of flooding, sieves have been installed to filter currents and prevent granules from ending up in the environment.